Bir Bakışta Yalın Üretim Sistemleri
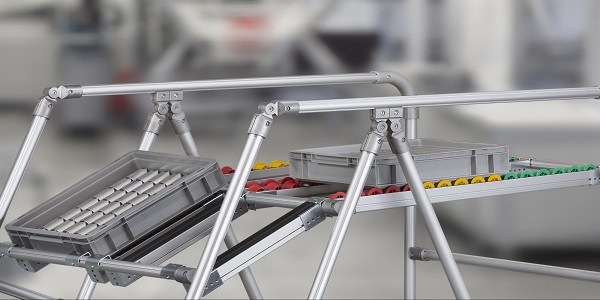
Yalın üretim terminolojisinin anlamı
Yalın üretim kavramları, doğrudan endüstriyel işlemlerde veya yalın yönetimde biraz değiştirilerek uygulanma konusunda başarılı olmaya devam etmektedir. Ancak konuyu yeni öğrenenler için sayısız ve hiçbir şekilde kendini açıklayaman terimler biraz kafa karıştırıcı olabilir.
İlk başta, çeşitli kısaltmalar ve / veya Japonca teknik terimler çekici görünmeyebilir. Ancak daha yakından bakarsanız, işlem optimizasyonu için etkileyici ve mantıklı fikirler keşfedeceksiniz. Bu blog yazısında, ana yalın üretim yöntemlerine kapsamlı bir genel bakış sunmayı amaçlıyoruz.
Sürekli iyileştirme süreci (CIP)
Sürekli iyileştirme süreci (CIP), tüm yalın üretim yöntemlerinin merkezinde yer alır ve endüstriyel bir ortama aktarılarak “Kaizen” kavramına dayanır. Bu anahtar Japonca terim “değişim” (Kai) ve “daha iyisi” (Zen) kelimelerinden oluşur. Buna göre, sürekli iyileştirme süreçleri, hataları açıkça kabul eden bir çalışma ortamı sağlamayı amaçlamaktadır. Bir şey düzgünce çalışmıyorsa, sinirlenmek için bir neden yerine, geliştirme fırsatı olarak algılanır.
Şunu unutmamak gerekir ki, iyileştirme süreci (CIP) majör hatalar için değil küçük detaylara yöneliktir ve hiçbir şey mükemmel değildir.
Bu bağlamda, iyileştirme süreci (CIP) herkesin duyularını kazanmayı amaçlar ve çalışanların katılımı bunu başarmak için hayati öneme sahiptir. Çalışanlar, süreçleri ilk gözlemleyen oldukları için yalın üretimde “gemba” olarak adlandırılan yerdedirler ve iyileştirme süreci konusunda en doğru yargılayan kişi konumdadırlar. Sadece yakından bakmak gerekir.
7 Muda: Atığın önlenmesi
Yalın metodolojinin bir diğer temel prensibi, kendi proseslerinizi optimize etmek istiyorsanız, atıkları aktif bir şekilde ele almanız gerektiğidir. Japonca'da “Muda”, değer yaratmaya yardımcı olmayan anlamsız bir faaliyet anlamına gelir. 7 Muda'ya göre atık, aşağıdaki şekillerde önlenebilir:
- Gereksiz yere malzemeleri hareket ettirmeyin
- Depo stoğunu azaltın
- Ergonomik olmayan hareketlerden kaçının
- Önlenebilir bekleme sürelerini azaltın
- İşlemeyi basitleştirin
- Sürekli geliştirin
Yukarıdaki liste, bireysel yalın üretim yöntemlerinin ne kadar iç içe geçtiğini açıkça göstermektedir. 7 Muda, sürekli iyileştirme ihtiyacı olan alanları tanıma konusunda temel yaklaşımlar sunmaktadır. Bununla birlikte, uygulamada atıklarla nasıl başa çıkılacağını da bilmeniz gerekir. Sadece farklı atık formlarını tanımak yeterli değildir.
Standart süreçler oluşturmak için 5S yöntemini kullanmak
CIP oldukça soyut kalırken ve kavramsal çerçeveyi sağlarken, 5S gibi yalın üretim yöntemleri pratikte neyin hayati olduğunu göstermektedir. 5S yöntemi, belirlenmiş bir zaman aralığında ve % 100 kalitede belirlenmiş bir çıktı sağlamak için işlemleri standartlaştırmaya yarar. Örneğin; 5S, üretim sürelerini azaltmaya yardımcı olan kararlı süreçler kurar. Ek olarak, standardizasyon sürekli iyileştirme için bir temel oluşturur. Toyota çalışanı Taiichi Ōno bir keresinde “Standartlar olmadan sürekli bir gelişme olamaz” demiş.
5S ismini, yöntemi oluşturan ve her biri Japoncada “S” ile başlayan bireysel kelimelere borçludur:
Seiri: İhtiyacın olmayan her şeyi kaldır.
Seiton: Çalışma malzemeni ergonomik olarak ayarla ve etiketle.
Seiso: Her zaman kendi çalışma alanını temiz tut.
Seiketsu: Düzensizliği önlemek için düzenli olarak temizleyin.
Shitsuke: Her zaman disiplinli ol.
5S'yi başarıyla uygulamanın çok sayıda yararı vardır. Montajda üretkenliği ve kaliteyi arttırmanın yanı sıra, çalışma alanlarını daha verimli kullanmak ve düzenli bir çalışma alanını sürdürmek genellikle çalışan motivasyonunu da artıracaktır. Bir sonraki müşteri ziyaretinizi istediğiniz zaman, kötü sürprizler olmadan düzenleyebilirsiniz.
Poka-Yoke ile belirli hatalardan kaçınmak
Sürekli gelişim fikri her şeyi güzelce özetler. Asla mutlak mükemmellik elde edemezsiniz, ancak denemeyi bırakmaya gerek yoktur.
item Academy’i Keşfedin!
İstediğiniz zaman ve istediğiniz yerde!- Uzmanlığınızı geliştirin
7 Muda - Atık Türlerini Tanıma ve Çözme
Muda (işe yaramaz faaliyet) şüphesiz en bilinen yalın üretim terimlerinden biridir. Şirketlerin Muda'ya çok fazla dikkat etmeleri ve Mura ile Muri'yi…